|
Post by acollins on Jan 18, 2014 15:09:59 GMT -5
Hey folks,
Not sure if this is the right area to ask this question, but I'll ask anyways.
I am getting ready to have custom decals made for my fictional line but have hit a stump with designing a logo.
Is there somone here that is good with small logo design and be willing to help out with this?
Thanks in advance,
Alex
|
|
|
Post by icghogger on Jan 18, 2014 17:55:24 GMT -5
What I have done is visualize a name (the Leaf River Railway, for example) and create a picture based on the words. In my case, I picture a leaf outline in in green, with the veins and stem of the leaf in blue, representing a river. Or turn the initials of your railroad in to a design (such as the "worms in love" design of the Penn Central). Keep working with it until you like what you see, but try to keep it simple (no more than two colors).
My own railroad name, while not fictional, incorporates elements of its name, the Gulf & Ship Island Railroad, which was a port railroad in south Mississippi. Its slogan was The Deep Water Route, which I combined with a ship's wheel to create the logo shown in my avatar.
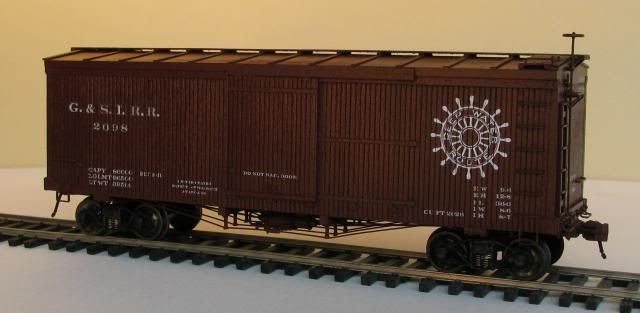
|
|
|
Post by jeff323 on Jan 18, 2014 19:16:54 GMT -5
PM me Alex, maybe i can give you a hand
|
|
mkl194
Trainmaster
accelerating rust on purpose
Posts: 131
|
Post by mkl194 on Sept 1, 2014 11:58:15 GMT -5
2 things I've learned with custom decals might help you out...
1. Even with my commercial printers, light colors often end up too transparent against most background colors...
2. Using white decal paper requires an almost impossible amount of trimming with a knife.
3. I purchased a Cricut Explore and used that for cutting with awesome results on white decal paper where objects aren't super complex at the edges. One of the best results is to print a block of color using the hi-res printer and then having the Cricut cut the decal, especially good with small numbers and small letters
If you use a service to do it for you, you won't need to worry about transparency. They should do it right with no problem.
When designing custom graphics, it's important to use a program that supports transparency when exporting. The best formats are SVG, PNG32 and TIFF/w transparency. Also it helps if you use CMYK when you design the grpahics.
|
|
|
Post by railfansd40t2 on Sept 4, 2014 19:17:39 GMT -5
Being an ex Graphics Designer and large format digital printer technician please remember that you don't just push a couple of buttons on the key board and magic comes out of the printer. Be prepaired to make lots of changes to the design to get things to print and apply correctly as well as pay for someones time because trust me when I tell you that if it was as easy as some people would like to think it is everyone would be doing it. There have been designs I have knocked out very quickly and had great results and the customer was happy, then there were the ones I spent MANY hours on to get the colors just right. Then there are the nightmare ones that never come out right and you loose your shirt on, and forget about how long it can be to recreate something that has been drawn on a napkin with a sharpie then scanned and oh yes matching font styles can be a real blast too.  Yes it is true that if you keep it simple from the beginning things can go pretty quickly but for the ones that are complex and different from what everyone else has there is time and effort involved which a lot of people will shy away from because of the cost or again they don't understand what goes into to it to make it work or look perfect when it is finished. You also have to keep in mind the limitations of the printer and if the artwork is either vector or raster there is a huge difference and it can have very different end results. These are just a few things to remember when you are trying to make your logo different and appealing to both you and others that will view it. Taking the time to think about how the logo will be printed as well as what it will be printed on will serve you well. Yes the inks from an inkjet printer be it large or small cheezo or high dollar are translucent and opacity is only obtained by printing on white material, or with white ink (costly) or on clear going over a white area. Just my two cents worth. Paulie
|
|
|
Post by stevef45 on Sept 5, 2014 4:11:54 GMT -5
I had a guy who is on here completely do custom decals for a project of mine. He put in nearly 20 or 30 hours of his time to design the stuff based off of prototype pictures, drew totally new cars like what you see from the railfan paintshop just so he can mock up them. Its not easy. If you have the artwork done, it will be a little easier for the printer like highball graphics, but even then he still does test prints to make sure things come out good.
|
|
|
Post by railfansd40t2 on Sept 5, 2014 10:43:59 GMT -5
That is the best way to do it. I have done the same and also taken photos of a customers vehicle scaled it and put the proposed artwork on that scaled photo then print it out as a proof sheet. There is no better way to show your customer what something is going to look like than it being on there actual vehicle or on a scaled drawing of say a locomotive or rolling stock and doing it in color is the real winner because then they can decide if it truly is what they want. This s no different then a paint chip or color swatch because a visual is worth a thousand words. I do this same thing when doing my projects so I know everything will fit correctly. You cant guess at it and don't ever assume that both sides of something are the same! Always take pictures of both sides to be sure things will fit where you want them to. I take pictures of the locomotive on both sides scale it, draw out my design or logo then print the artwork on paper in gray scale test fit it to the actual item it is going on make any adjustments it may need then work on the colors to get them right and finish up with the final printing.
20 to 30 hours is pretty common when working from a photo and recreating it. This is where it starts to get costly, then you factor in the color corrections and the hours start to add up. If the prototype photo is not real good you open up another can of worms. I sent some artwork to a printer completely separated by color and all vector in the file format he uses so there was nothing for him to do but output it to the printer and those decals were going to cost me $30.00 plus shipping for one full 8 1/2 x 11 sheet. That is not really a bad price but if he had done all the work I did that price easily could have doubled or even tippled depending on if I couldn't provided him with the correct fonts or ones that were converted or a vector image to start with. Raster images are made up of pixels and if not clean to start with can be a pain for many reasons and can run up the bill to make them usable very quickly. If someone is starting from scratch for you based on an idea you have there can be much less time and work involved but again it all comes down to the complexity of your idea for that logo. If you are trying to recreate something that is in the real world but not available remember they call it custom for a reason and the price will reflect that.
Paulie
|
|
|
Post by m a y o r 79 on Sept 5, 2014 12:04:48 GMT -5
1. Even with my commercial printers, light colors often end up too transparent against most background colors...
Very true. I went the cheapo route and printed out my own custom decals on clear decal film, the lettering was in orange and it looked really good....on the decal paper. Once I put it on a black painted locomotive the lettering almost completely disappeared! I ended up reprinting everything on white decal film with black boxes around everything. Once the decals were in place and the model slightly weathered you couldn't see the black decal film outline anymore. I got lucky though that my main body color was black, if it was a custom color matching the paint to the printed color on the decal film would be almost impossible.
|
|
jiml
Probationary Member
Posts: 2
|
Post by jiml on Aug 25, 2015 19:55:33 GMT -5
2 things I've learned with custom decals might help you out... 1. Even with my commercial printers, light colors often end up too transparent against most background colors...
But, this is not a problem with the "professional" printers? Do I understand you correctly?
I am thinking of putting white decals onto red paint. Either a bright red such as that on Canadian Pacific diesels, or a perhaps a darker "scarlet" such as that on Southern Pacific engines.
I was going to use stock "barricade" decals from Microscale, and custom made decals from Railgraphics in Illinois. All in white. It is for a fictitious railroad I'm designing/building.
Do you think I may have problems using these white decals? Too transparent for the red?
I am a novice to detailing/painting/decaling, and want to make it easy at first. I could change the decal color from white to black, I guess.
Much thanks Jim
|
|
|
Post by emd16645 on Aug 25, 2015 20:20:29 GMT -5
If you are using custom decals from a company such as rail graphics or highball, they can print in white just fine for whatever background you need.
|
|
pacbelt
Chairman
Building Layout #11!! ;)
Posts: 682
|
Post by pacbelt on Sept 14, 2015 10:43:07 GMT -5
These are my WHITE decals....(the black area is left clear on the decal) 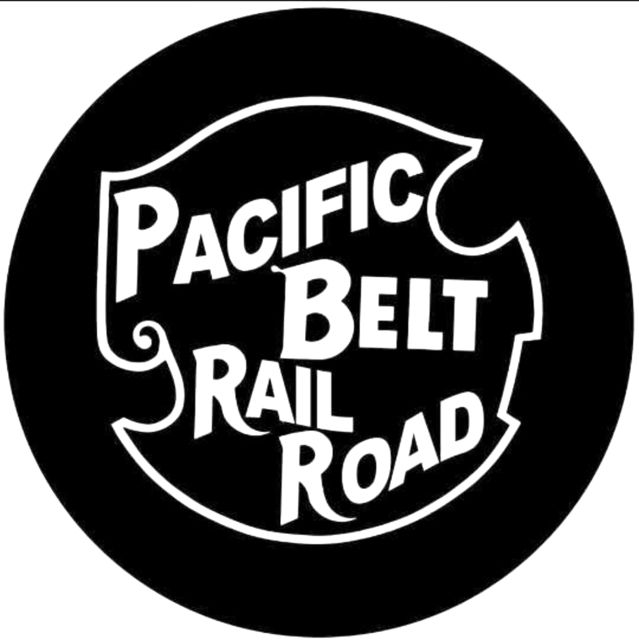 If you can spend $4-550.00 on an ALPS Printer, you can do brilliant whites and light tones, and silver & gold! I couldn't, but have a friend in Australia willing to print them for me. The herald was designed starting with the "Cotton Belt" herald.
|
|
|
Post by jwhite07 on Nov 1, 2015 13:05:38 GMT -5
If you can spend $4-550.00 on an ALPS Printer, you can do brilliant whites and light tones, and silver & gold! I couldn't, but have a friend in Australia willing to print them for me. I bought an ALPS close to when they first became known to the hobby market (fifteen years ago or so?) and got many years of use out of it... luckily long enough that most of my own custom decal printing needs were fulfilled before it started to operate erratically. I still have it and keep an old computer to run it on. By now, though, it works very poorly (major issue is a intermittent but increasingly frequent carriage return motor failure, and occasional registration lines across a print). For all intents and purposes it's pretty much dead; stuff wears out, and I don't have much in the way of supplies left for it, but it has been a great tool. I'll hang onto it just in case, so don't ask - it is NOT for sale. Yeah, reconditioned ALPS are available, but it's harder and harder to find ALPS cartridges now - they are getting very rare and more often are priced that way too (I once saw a seller asking $1,000 for a single white cartridge. Yeah, riiiiiight, buddy). Unfortunately there doesn't seem to be much market for a follow-on to that kind of printing technology for the home. Too bad, but in the meantime, as mentioned there are some pretty good commercial printing shops out there.
|
|
|
Post by iomalley on Nov 1, 2015 16:47:53 GMT -5
I ran one commercially for awhile (does anyone remember SGSDecals?) and the Alps was a painful way to run a business. I went through 4 printers in the 6 years I was printing decals. The last year (2004) there were alot of them coming up used but they either had print heads that no longer generated enough heat to stick the ink, or the shuttle was losing register. I traded my last printer and cartridges last year for a resin truck model because it was such a PITA to run the printer with a hybrid driver that would work on Windows XP.
I gave all my artwork to Jim at Highball to keep them alive, but even Jim is looking to screen print his more popular sets. I have a screen printer near Toronto that will do decals too. The challenge is really finding someone who I can hand my print-ready Adobe Illustrator file to run with it.
The Alps was cool, but it was marketed for the niche sticker or labelmaker and didn't catch on because changing 4 cartridges through a print cycle was pretty silly for someone who didn't need white, and it was SLOW. Some technology just refuses to go desktop.
|
|
pacbelt
Chairman
Building Layout #11!! ;)
Posts: 682
|
Post by pacbelt on Nov 2, 2015 0:36:04 GMT -5
I hear ya ... I am surprised that NOBODY is bothering to make a current technology compatible, white and metallic printing printer ! SURELY there must be some market for it, right?
ALPS was far from perfect, but it did the job. I guess finding a silk screener willing to do small runs, is our only best option....
~ Carmine
|
|
|
Post by iomalley on Nov 2, 2015 10:07:41 GMT -5
What I would suggest, is coming up with a decal set that the masses will buy, especially if its a set that correct's Microscale ills, and maybe 3 or 4 sets will fit on a ltr sized sheet, and the bottom inch of the sheet is your fictitious decals. While you cut up and package your 'sellable' sets, the trimmings have the custom stuff you need....free! You will pay screen cutting prices for each colour, anywhere from $50 to $100 a screen. Sheet costs are cheap, but usually carry a minimum run. My last set, CN diesels, my costs were around $900 for 300 sheets, and I made around $1200. Not bad, unless you consider the hours I put into the artwork. The artwork components were a culmination of years or different sets of work, but at least I didn't go into the red. I've already purchased the screens, so now if I run more, my sheets costs are the only consideration! Something to consider. It requires copius amounts of research to get your sellable set right though. If you half a$$ it, it won't fly.
|
|
|
Post by netzlofdesign on Nov 9, 2015 12:25:20 GMT -5
On the subject of decals:
The problem for many home road and freelanced lines for ages has been white- not only as it's self, but the ability to print white under color for a more opaque appearance. ALPS was a (temporary) solution to the problem, but as we're seeing now supplies of ink and the printers themselves are dwindling and will soon be completely unavailable. Other printers that can print white do exist, but their cost is a limiting factor; no longer can the home hobbyist send $500 away and have a decal machine show up. Commercial printers, such as myself, should know to perform test prints and should also be aware of the limitations of their preferred printing method in regards to colors, and opaqueness. While I cannot actually speak for anyone else, I never stop experimenting with my printer to learn about what it's actual limits are; but I never play the odds with a customer order, be it decals or direct printing.
About Logo Design: Designing a logo for a freelanced home road can take multiple turns based on decisions and wants. Some folks want something that could easily be confused with an actual railroad, some want something that lines up more with modern graphic designed logos, and still others want something completely off the cuff or for fun. Knowing this first, I'm able to better determine what kind of research is needed to begin the project. Taking the ultra-prototypical view point for example, I prefer to know the operating area, era, principle commodity, and any other details that are available before setting down to design a logo/paint scheme that will feel "right" for the railroad. A line operating in Florida would more than likely not feature a Ponderosa Pine in the logo, much the same as a line from Maine would not feature an oil field pump jack.
I've had several customers who have arrived with artwork in hand, as well as several who have no idea what they're looking for, just a basic description. I do offer "branding" assistance for model railroads, but as I don't wish to turn this into a sales pitch I won't be discussing any further specifics in this post.
|
|