mkl194
Trainmaster
accelerating rust on purpose
Posts: 131
|
Post by mkl194 on Dec 7, 2015 15:11:44 GMT -5
I need help from someone who knows how to make molds.... I want to make a mold of the FB-2 sideframe below so I can replace all the horrible sideframes on my Bachmann Plus locomotives.... This comes from a B23-7. It will fit pretty much every cheap Bachmann locomotive made way back when. I've been working hard on a number of U36B's that I want to upgrade. I just can't grasp the technique to make this thing 1 piece. I have Alumilite to make the what I assume will be a 2 part mold, but I need someone to describe the process to make a mold of this thing.... Here it is:  Here is another view:  So how can this be done? I want to make a bunch of these things...
|
|
|
Post by iomalley on Dec 7, 2015 17:05:57 GMT -5
Hey MK; Its not a simple process, if fact it gave my mould maker a bit of head-scratching to achieve. I had these made up in one piece too. 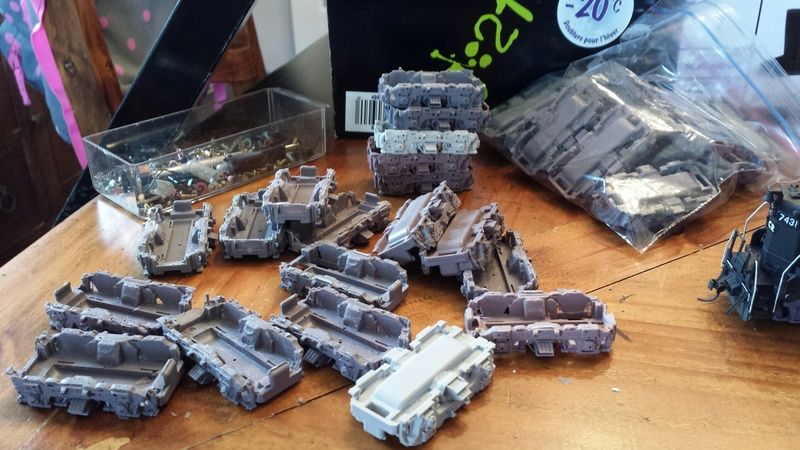 He had to fill across all the open holes within the casting, bridging across the wheel openings with tape. You can just see it in the photos. It can be done, as Barry had did for me, but Barry's been casting for 10+ years and even he saw it as a challenge. Talk to Barry over at Railrec.com and he'll be able to give you some insight I'm sure.
|
|
mkl194
Trainmaster
accelerating rust on purpose
Posts: 131
|
Post by mkl194 on Dec 7, 2015 17:22:19 GMT -5
This is the project that gave me the idea that it could be done, I'm just not good with multi part molds
|
|
mkl194
Trainmaster
accelerating rust on purpose
Posts: 131
|
Post by mkl194 on Dec 21, 2015 15:34:58 GMT -5
I've tried twice now to mold this piece, both times a failure. The last time I tried a 2 part Alumilite RTV mold and the open spaces were just too much. I sort expected that to happen, but I wanted to find out what the problems would be.
I'm thinking of trying again, this time will mold putty on the inside first with over hanging ledges. Then flipping it upside down and using "remold" for the outside.
Anyone have any useful tips?
|
|
|
Post by areibel on Dec 21, 2015 18:49:21 GMT -5
I'd try a three part mold. Fill the center of the sideframes (where the gear case would be) with clay (low sulphur kids clay works great). have it extend up in a column about 3/4 or 1 inch above the top of the plastic and I'd let it flare out. That way when you pour your plastic and drop the center plug back in it will keep the center from dropping down too far and making the bottom plate too thin. You'll need a mold box of some sort, I use some of those big Lego style blocks (I use those cheap bigger ones, they work fine). Suspend it on it's side by sticking a rod or dowel in the clay, then pour in the rubber so it's about half way up the base plate, make sure the outside edge ( the bottom of the pour) isn't too thin, I'd keep it at least a half inch thick. Let that cure fully, then remove it from the mold box. Then set it upright, build a new mold box around it and keep it supported. Coat the exposed rubber with mold release or the rubber halves will stick together, I just make my own out of Vaseline cut with mineral spirits so it's not too thick and brush that on or you can use a ready made spray. Pour the other half and let it cure. Once it's ready, separate the halves, remove the clay and coat everything with the mold release. Then fill the void that left from the clay with the rubber and let cure. I should have mentioned to leave a couple small vents, a couple toothpicks glued to the inside of the sideframes. Try to locate them at a high spot like the inside of the axle ends, it helps let the air and excess plastic escape. When I pour the plastic I usually leave the mold in the mold box, it helps keep it more rigid so it doesn't flex and get goofy. I get my stuff from Smooth On, www.smooth-on.com/ . They have a ton of videos to help you get started, and a great tech support you can call with questions. This is a real basic explanation, watch some of the videos and give it a try! Good Luck! Al
|
|
mkl194
Trainmaster
accelerating rust on purpose
Posts: 131
|
Post by mkl194 on Dec 22, 2015 10:20:34 GMT -5
That's a brilliant idea
|
|
|
Post by areibel on Dec 22, 2015 18:59:01 GMT -5
LOL! Not brilliant (or I would have done it that way the first time I did it), just lots of trial and error! You just have to think where you DON'T want a possible mold line to wind up- If you make it in two halves then any parting line or flash will be up the middle of the base plate and should be pretty easy to remove. Same with the clay on the inside, you want to block any rubber from getting inside but make it smooth on the outside and keep it as flush to existing plastic as you can. And watch for undercuts, where the mold can have a spot that might trap air and keep plastic from filling the details. That's where the vents help, it also helps to pour in the plastic, pick up the mold and rotate it around carefully so all the detailed areas get coated before you put the center plug in.. I enjoy tinkering with it, you'll learn a lot by just trying different things.
|
|
mkl194
Trainmaster
accelerating rust on purpose
Posts: 131
|
Post by mkl194 on Dec 23, 2015 13:59:14 GMT -5
So my first attempt was a total failure...fortunately I was trying to practice and learn what would be needed before I used expensive RTV to make the mold. I made the clay plug easy enough. I made a mold box of large legos hot glued to glass. Then I used Alumilite Remold for the practice run.
Remold is heated in the microwave for about 30 seconds in a simple ashtray and poured into the mold box. No problems with the first half. It's accurate and strong.
Then I setup for the second half. I should have guessed before I poured that part that the remold can't be used for 2 part molds like that. It fuses to itself even in the presence of a decent mold release. So I ended up making a mess. It also heated the clay plug making it really tough to clean out of the original.
Lesson learned. The concept was totally sound though. The other problem with remold is that it can lift up the mold box on the inside and seep underneath because.
This has given me an idea however. Remold melts at a low temp (which means no heat producing polymers can be poured into it) which could be useful in some other way.
Next I'm going to try Mold Putty to make the plug and use the RTV to make the mold halves...
|
|
|
Post by areibel on Dec 23, 2015 16:42:16 GMT -5
Well I wouldn't call it a failure, just some practice! A lot of the details I mentioned were from some pretty EPIC failures- mostly the venting and the mold release issues. I was trying to cast an HO scale boiler shell and shrink it to TT ( talk about wasted efforts!). I started by pouring the bottom half with the boiler upside down so the bottom of the mold is the top of the casting. The mold box was probably 10 inches by 4 by four, so lots of rubber! I gave it a quick spritz of the canned mold release and poured the top half of the mold (with no vents). It cured and I tried the first pour (with no vents)- most of the lower section of the ash pan and anything else thin wouldn't fill with plastic. Dang! Went back (in a hurry), stuck the original back in the mold (in a hurry) added a couple vents and re-poured the top half. Let it cure over night and found a new problem- NO MOLD RELEASE! I didn't use much the first time so it was a little sticky coming apart, but I didn't think to use any the second time and it was one big ole block of rubber with a boiler trapped inside. I tried cutting it out but made a mess and damaged the original boiler so the whole thing went in the trash!
Have you actually poured plastic into the Remold? I've wondered how it does.I'd read an article about it, maybe in MRH but it sounded almost too good to be true. I do a lot of odd ball and one of stuff so it sounds like it work well for that but I haven't gotten any to try. That, and I have to work in my basement ( the wife gets a bit perturbed when I take over the dining room table) and it's about 40 degrees down there now!
|
|
mkl194
Trainmaster
accelerating rust on purpose
Posts: 131
|
Post by mkl194 on Dec 24, 2015 10:51:47 GMT -5
Remold would be awesome for anything that doesn't make heat, and for 1 part molds it would be fantastic. Even with my failure, all the remold was recovered. The other nice thing about it is the ability to heat it again to make releasing the mold super simple, as long as you only need to make 1 part.
40 degrees would be a good working environment. The Remold melts in about 30 seconds, but takes a good hour or more to cure in 75 degrees. While it's still warm, it will left up hot glue and get under the mold wall and continue to flow that way.
The next time I use remold, I'm going to use all of it and pour it in a bowl for the mold box. Then I'll just trim away the excess and reuse it.
Where I can see remold being the best product is when using plaster of paris. I've never tried any other low temp casting material, but if you have any suggestions, I'll give it a try. I love finding new materials.
My next step is going to be doing the whole process over again. This time I'm going to thoroughly test the plug. Then I'm going to make a much higher quality mold box. It'll be about a week before the next attempt, but I'm going to watch the smooth on videos all over again...
|
|
mkl194
Trainmaster
accelerating rust on purpose
Posts: 131
|
Post by mkl194 on Jan 22, 2016 15:33:15 GMT -5
I'm not giving up on this one...I want those side frames.
I've gotten the mold putty and I also have Alumilite RTV.
The hardest part about this project to me seemed to be the construction of the mold box. Making the plug doesn't require a mold box. But when I used the legos to make the mold box for the other 2 parts I ran into the problem of the remold melting the hot glue used to secure the legos to the piece of glass. This isn't a problem with the RTV.
The problem is that RTV is too expensive to tolerate a lot of waste.
Next time I use remold, I'll line the box with plastic wrap first. Remold has some real potential though. It's too cheap not to have a tub of it around, especially if you use plaster of paris. 1 off molds take like 5 minutes to make and can just be recycled after use.
|
|